Challenge
Students and employees complain about the low temperatures, and service calls do not resolve the problems.
The public education center has suffered from space comfort problems for many years. Students and employees complain about the low temperatures. Every year, they have to call the HVAC control vendor and reset the terminal boxes’ heaters, sometimes two or three times, which increases the cost of operation.
Despite numerous service calls and troubleshooting attempts, the problems persist. Heaters have already been reset three times this year, and this seems to occur more frequently when outdoor temperatures are cold. They seek to understand why this issue persists and have reached out to our team for assistance.
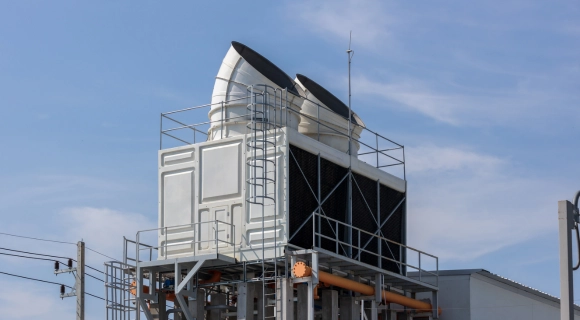
Scope of Work
The audit encompasses a thorough examination of the public education center’s building automation and HVAC control system. The goal is to identify root causes of the issues, including malfunctioning and incomplete sequences of operations, critical and poorly commissioned components, and potential fault detection indicators to notify building operators of equipment failures.
HVAC systems subject to the control audit:
- Fifty-one Single Duct Pressure Independent VAV Boxes with Electric Reheat Coil
- Three Multizone Air Handling Units with Chilled Water Coil
- Two Multizone Air Handling Units with Dual Coil (Chilled Water and DX)
- One Constant Water Flow Chiller Plant Comprising:
- Two Water Cooled Chillers
- Two Chilled Water Pumps
- One Constant Speed Cooling Tower
- Two Condenser Water Pumps
Audit Summary
Total Equipment Audited
Incomplete Sequences Detected
Equipment Deterioration Factors
Energy Waste Sources Identified
Fault Detection Possibilities
Non-Commissioned Components
The audit reveals that incomplete sequences of operations are the primary cause of the underlying problems. One significant finding is that the occupancy status of air handling units (AHUs) and terminal boxes (VAV) does not match. VAVs remain in occupied mode even when the units are off, potentially causing heater’s thermal protection to trip, requiring a reset in cold weather.
Additionally, critical components require commissioning, and energy is wasted due to manual overrides and inefficient sequences of the AHUs and the Chiller Plant. It is estimated that 35% to 55% of energy is wasted in the overall system.
Critical Items
- Both Water Cooled Chillers run simultaneously 24/7, resulting in significant energy waste.
- Both Chilled Water Pumps and Condenser Water Pumps operate continuously, indicating further energy waste.
- Two Air Handling Units operate continuously, contributing to energy waste.
- Operation of Dual Coil Air Handling Units needs verification as DX coils are not functioning.
- Humidity control is lacking, as there are no sensors in the VAVs or AHUs to monitor space humidity.
- Many components require commissioning, including pressure sensors, valves, frequency drive controls, control dampers, and compressors’ commands.
- Operational points are overridden and fixed, leading to low performance and efficiency.
- All VAV boxes require zero calibration, and their operation bands can be optimized for better performance.
- None of the VAVs have discharge air temperature sensors, which could aid in monitoring heater status.
- The Building Management System (BMS) front-end user interface (UI) requires improvement, with trends, fault detection panels, and operational setpoints and bands missing.
Recommendations
- Address all identified energy waste sources to achieve a 35% to 55% reduction in HVAC power consumption.
- Recommission all units and critical components for proper operation.
- Complete, test, and optimize all unit sequences of operations for improved performance and efficiency.
- Conduct an indoor air quality (IAQ) test and integrate ventilation and humidity control mechanisms for enhanced space comfort.
- Implement fault detection mechanisms to anticipate future failures.
- Update the BMS user interface for better visibility and control for operators.